How to Choose a Pigging System: A Step-by-Step Guide for Manufacturers and Engineers
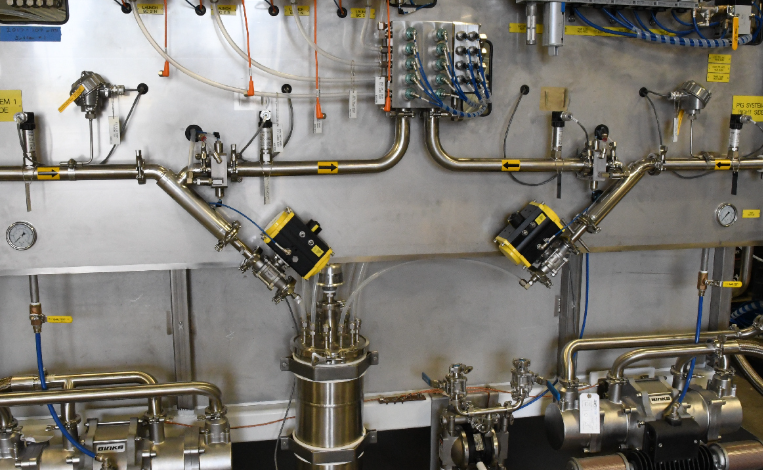
In today’s competitive industrial landscape, efficiency, sustainability, and cost-saving technologies are more vital than ever. One such innovation—pigging—has revolutionized pipeline operations across sectors like food and beverage, cosmetics, chemicals, and pharmaceuticals. But knowing how to choose a pigging system is not always straightforward.
From product recovery and hygiene to automation and safety, there are many factors to consider before investing in a pigging system. A poorly chosen system may underperform or be incompatible with your existing setup, leading to lost resources and poor ROI.
This guide walks you through the essential considerations and decision-making steps in selecting the right pigging system for your business operations.
What Is a Pigging System?
A pigging system uses a device called a “pig” that is inserted into a pipeline to push residual product through to its destination. In modern systems, this process can be automated and designed for tasks such as:
- Cleaning the pipeline interior
- Recovering product that would otherwise be wasted
- Reducing water and cleaning chemical use
- Minimizing changeover time
- Preventing cross-contamination
Pigging systems are especially valuable in industries that deal with viscous or high-value liquids, frequent product changeovers, or strict hygiene requirements.
Why the Right System Matters
Choosing the correct pigging solution means better product yield, faster cleaning, improved operational flow, and safer handling. The wrong choice, however, could result in operational inefficiencies, unexpected downtime, or even product loss and contamination.
That’s why understanding how to choose a pigging system is essential to making a sound, strategic investment.
See also: self loading concrete mixer: The Evolution of Concrete Mixing Technology on Wheels
Step 1: Understand Your Product and Process Requirements
Start by thoroughly analyzing your pipeline application:
- Type of Product: Is it thick or thin? Sticky or abrasive? Acidic or sensitive to contamination?
- Product Value: High-value products increase the importance of recovery rates.
- Frequency of Changeovers: If you switch products often, pigging becomes even more beneficial.
- Sanitary Requirements: Food, beverage, and pharma industries must meet strict standards.
Knowing your product’s characteristics helps determine the type of pig, material compatibility, and design of the pigging system that will work best.
Step 2: Assess Your Pipeline Configuration
Pigging systems must be designed to match your existing infrastructure.
- Pipeline Length and Diameter: Pigs must match these dimensions to maintain tight seals and proper movement.
- Bends and Elevation Changes: Some pigs struggle with sharp turns or vertical sections.
- Number of Lines: If you have multiple pipelines, you may need a system that can pig several lines or switch between them.
- Connection Points: Pig launchers, receivers, and sensors must be integrated without disrupting production.
An experienced pigging system supplier will assess these factors and design accordingly.
Step 4: Choose the Right Type of Pig
Pigs come in a variety of materials, shapes, and functions.
- Solid Pigs: Durable and best for high-pressure or abrasive products.
- Foam Pigs: Flexible and good for navigating tight bends.
- Gel Pigs: Best for scrubbing or removing deposits.
- Smart Pigs: Equipped with sensors for inspection and data collection.
- Sanitary Pigs: Designed for clean-in-place (CIP) systems in food or pharma production.
The right pig should suit both your product and pipe material while being easy to clean or replace.
Step 5: Consider Safety and Cleanability
Safety is critical, especially with pressurized systems or hazardous fluids.
- Pressure Ratings: All components must match your operating pressure to avoid failures.
- Pig Detection Systems: Track the pig’s position to prevent accidents or misfiring.
- Cleanability: Parts that contact product should be hygienically designed and easy to sanitize.
If you’re in a regulated industry, these factors are essential to comply with standards like FDA, GMP, or EHEDG.
Step 6: Evaluate Maintenance and Support Requirements
Pigging systems may require occasional maintenance—especially in automated setups.
- Ask providers about:
- Spare parts availability
- Maintenance frequency
- Software and firmware updates (for smart systems)
- Technical support response times
Choose a provider that offers strong post-sale support and training. Knowing how to choose a pigging system also means choosing a company that stands by their technology.
Step 7: Analyze Cost vs. ROI
While pigging systems can represent a significant investment, the long-term returns are often substantial. Assess the cost against:
- Product recovery value
- Cleaning time saved
- Labor cost reduction
- Downtime avoided
- Water and chemical savings
In most cases, a well-designed system pays for itself in under two years. But this varies depending on your operation’s scale and efficiency goals.
Step 8: Choose the Right Vendor or Integration Partner
Not all pigging system providers are created equal. Choose a company with:
- Proven experience in your industry
- Custom design capabilities
- Solid client references or case studies
- Strong training and support packages
- Commitment to safety and compliance
Many manufacturers now seek turnkey solutions—so find a partner who understands your full process, not just the pipeline.
Bonus Tips: Questions to Ask Before You Buy
- Can the system handle my product’s viscosity and temperature?
- Is the pig material compatible with my product and pipe?
- Will the pig reach every part of the pipeline?
- How is the pig detected and controlled?
- Can the system scale with future expansions?
These questions help clarify your needs and ensure the system can evolve with your business.
Conclusion
Knowing how to choose a pigging system is crucial to ensuring optimal efficiency, safety, and profitability in your operation. From evaluating product and pipeline specifications to selecting the appropriate pig and automation level, every decision plays a role in performance and ROI.
With thoughtful planning and the right partners, your pigging system can deliver long-lasting value, reduce waste, and transform your production process. In a world focused on sustainability and precision, pigging isn’t just a smart move—it’s the future of liquid handling.