Why Sheet Metal Stamping Services Are the Backbone of Modern Manufacturing
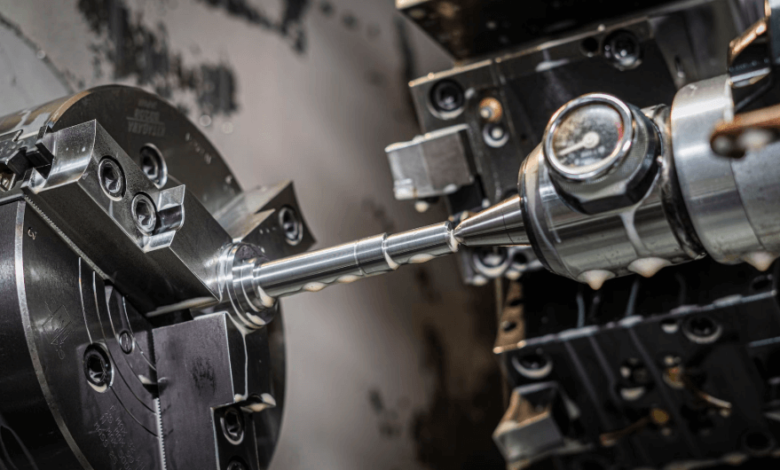
From the car you drive to the appliance you use daily, sheet metal stamping services play a vital role in shaping the components that keep our modern world running smoothly. With increasing demand for precision, efficiency, and cost-effectiveness, industries across the globe are turning to specialized metal stamping to meet production goals while maintaining high-quality standards.
In this comprehensive article, we explore what sheet metal stamping is, its applications, advantages, and how to choose the right service provider for your business.
What Are Sheet Metal Stamping Services?
sheet metal stamping services refer to the process of shaping flat metal sheets into specific designs or forms using high-tonnage presses and customized dies. These services involve a range of operations such as:
- Blanking – Cutting raw sheets into base shapes.
- Bending – Creating angles or curves.
- Punching – Adding holes or slots.
- Embossing – Imprinting logos or patterns.
- Deep drawing – Forming complex three-dimensional parts.
The objective is to produce accurate, repeatable, and cost-efficient metal components used in everything from simple brackets to intricate aerospace parts.
See also: self loading concrete mixer: The Evolution of Concrete Mixing Technology on Wheels
Why Are Sheet Metal Stamping Services So Important?
Sheet metal stamping has evolved into one of the most essential production methods in industrial manufacturing for several reasons:
1. High Efficiency
Once tooling is set up, thousands or even millions of identical parts can be produced at high speeds, significantly reducing unit cost.
2. Precision
Advanced machinery allows for extremely tight tolerances, ensuring components meet exact specifications critical to industries like automotive and medical.
3. Versatility
These services accommodate a variety of metals such as stainless steel, aluminum, copper, brass, and even high-strength alloys.
4. Customization
Through CNC technology and CAD/CAM design, parts can be customized to suit highly specific use cases without sacrificing efficiency.
Industries That Rely on Sheet Metal Stamping Services
The adaptability and scalability of sheet metal stamping services make them indispensable across a wide range of industries:
Automotive
From door panels to engine brackets and fuel system components, stamping ensures uniformity and strength in high-stress environments.
Aerospace
Aircraft manufacturers rely on lightweight yet durable stamped components for internal structures, ventilation, and control systems.
Electronics
Connectors, heat sinks, and mounting brackets are produced with tight tolerances to fit within compact circuit boards and enclosures.
Medical Devices
Surgical instruments, braces, and implantable components require clean finishes and precision that metal stamping can consistently deliver.
Consumer Goods
Household appliances, kitchenware, and furniture parts are commonly shaped using sheet metal stamping processes.
Common Materials Used in Sheet Metal Stamping
Depending on the industry and application, sheet metal stamping services may work with a variety of materials. Some of the most commonly used include:
- Stainless Steel – For corrosion resistance and strength.
- Aluminum – Lightweight and easy to form, ideal for aerospace and electronics.
- Copper – Offers excellent conductivity, used in electrical components.
- Brass – A good option for decorative hardware and fittings.
- Cold Rolled Steel – Affordable and strong, often used in automotive parts.
Material selection is a crucial aspect of the stamping process, influencing the design, die selection, and overall performance of the finished part.
Types of Stamping Operations
The right stamping process depends on your component’s complexity, quantity, and material. Key methods include:
1. Progressive Die Stamping
This involves feeding a coil of metal through a series of dies. Each station performs a different operation until the part is complete. It’s ideal for high-volume production.
2. Transfer Die Stamping
Similar to progressive stamping, but individual parts are moved from one station to another using mechanical transfers. This is better for larger or more complex parts.
3. Deep Draw Stamping
This allows flat metal to be formed into a hollow shape (like a can or enclosure) in one or several strokes.
How to Choose a Sheet Metal Stamping Service Provider
To ensure you’re working with the right partner, consider the following criteria:
1. Industry Experience
Look for companies with a proven track record in your specific industry. For example, aerospace stamping requires different standards than consumer appliance parts.
2. Tooling Capabilities
Strong in-house tool and die capabilities ensure fast prototyping and repair, reducing production delays.
3. Material Expertise
Make sure the manufacturer can work with your desired material and offer guidance on its suitability for your application.
4. Technology and Equipment
Check if they use modern CNC presses, servo-driven machines, and 3D inspection systems for consistent quality.
5. Production Volume Support
Whether you need 100 units or 10 million, the service provider should be able to support your required volumes efficiently.
6. Certifications
Look for ISO, IATF, or medical-grade quality certifications depending on your product category.
Future Trends in Sheet Metal Stamping
With digital transformation sweeping the manufacturing industry, sheet metal stamping services are also evolving. Here are some innovations shaping the future:
– Smart Tooling
Tooling systems now incorporate sensors that collect real-time data on tool wear, pressure, and part quality, enabling predictive maintenance.
– AI and Automation
Artificial intelligence and machine learning algorithms can detect anomalies, reduce waste, and streamline production in real time.
– Eco-Friendly Stamping
Manufacturers are investing in energy-efficient equipment and recycling systems to reduce their carbon footprint and promote sustainable practices.
– Rapid Tooling
Additive manufacturing is now being used to create prototype tooling, drastically reducing lead time for new part development.
Common Challenges in Sheet Metal Stamping (And How to Overcome Them)
While versatile, stamping does come with challenges:
- Tool Wear and Downtime: Over time, dies wear out and may cause dimensional inaccuracies. Regular maintenance and quality tooling materials mitigate this risk.
- Burr Formation: Improperly designed or dull tools can leave sharp edges or burrs. Secondary finishing or tool sharpening can address this.
- Springback Issues: Certain metals may return to their original shape after bending. Adjusting die angles or using forming simulations can help counteract this.
Professional sheet metal stamping services include process optimization to minimize such defects and ensure high-quality output.
Final Thoughts
As the demand for precision, speed, and customization grows across manufacturing sectors, sheet metal stamping services remain indispensable. Whether you’re a startup developing new consumer electronics or a global automotive supplier, choosing the right stamping partner can define the success of your production.
With proper planning, collaboration, and selection of the right service provider, you can achieve superior part quality, reduce costs, and meet demanding timelines—all while scaling your production confidently.