CNC Machining: The Backbone of Modern Precision Manufacturing
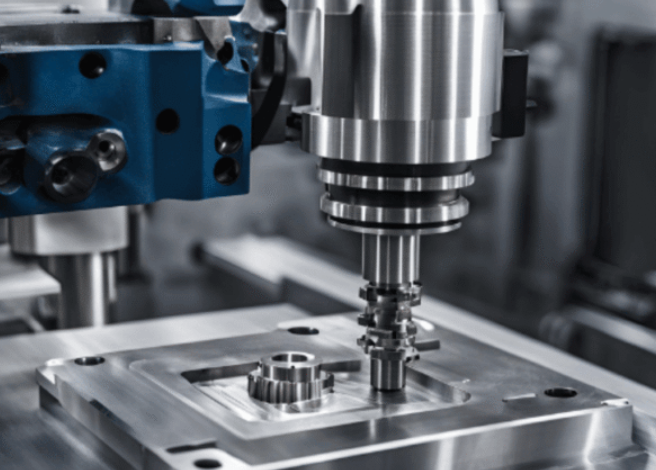
In a world driven by innovation, speed, and accuracy, cnc machining has become the cornerstone of modern industrial production. From aerospace components to smartphone enclosures and medical implants, the demand for highly precise, repeatable, and reliable parts has made CNC (Computer Numerical Control) machining a dominant force in global manufacturing.
This article explores the essential role of cnc machining in today’s industries, its core technologies, benefits, applications, and how businesses can leverage it for growth and competitive advantage.
What Is CNC Machining?
CNC machining is a subtractive manufacturing process where computer-controlled machines remove material from a solid block (also known as a blank or workpiece) to create a desired shape or part. The machining process is guided by coded instructions (G-code) derived from a CAD (Computer-Aided Design) model.
This automation enables complex geometries and tight tolerances to be achieved with incredible precision—often within microns. The most common CNC machines include:
- CNC Mills: For cutting and shaping solid materials.
- CNC Lathes: For rotational cutting.
- CNC Routers: Typically used for softer materials.
- CNC EDM (Electrical Discharge Machining): For hard or heat-sensitive metals.
- CNC Plasma and Laser Cutters: For sheet metal and non-metallic materials.
The Evolution of CNC Machining
CNC machining services has evolved from manual tool operation to computer-aided precision control. The concept dates back to the 1940s, when early forms of numerical control were developed. The real revolution came with the integration of microprocessors and computer systems in the 1970s and 1980s.
Today’s machines are smarter, faster, and integrated with software tools that allow real-time monitoring, feedback loops, and predictive maintenance. This evolution has reduced human error, increased efficiency, and dramatically cut production lead times.
See also: Exploring the Role of 18662719305 in New Age Tech Solutions
Benefits of CNC Machining
Choosing cnc machining over traditional fabrication methods brings several distinct advantages:
1. High Precision and Accuracy
Modern CNC machines can operate with tolerances as tight as ±0.001 mm, making them ideal for industries that demand extreme precision, such as aerospace, defense, and healthcare.
2. Consistency Across Production Runs
Once a part design is programmed, it can be reproduced hundreds or thousands of times with no deviation. This ensures consistency across large batches.
3. Efficient Turnaround Times
With automation and minimal manual intervention, cnc machining can significantly reduce production time—especially for prototypes and short runs.
4. Material Flexibility
CNC machines can process a wide variety of materials, including:
- Metals: Aluminum, steel, titanium, brass, etc.
- Plastics: ABS, PEEK, nylon, Delrin.
- Composites and exotic alloys.
5. Reduced Waste
Precision cuts mean less material is wasted, resulting in cost savings and improved sustainability.
6. Lower Labor Costs
Since CNC machines require fewer operators and minimal manual input, the overall labor cost is significantly reduced compared to manual machining.
Industries That Rely on CNC Machining
Cnc machining is not restricted to one field—it’s used across nearly every manufacturing sector. Here are some major industries that depend on it:
- Aerospace: Producing turbine blades, engine components, and structural brackets.
- Medical: Surgical tools, orthopedic implants, and dental devices.
- Automotive: Engine housings, brake system parts, custom mods.
- Consumer Electronics: Casings, heatsinks, connectors.
- Oil and Gas: Valves, pumps, and precision drilling tools.
- Defense and Military: Firearms components, navigation hardware.
Each of these sectors requires tight tolerances, material strength, and the ability to scale—making cnc machining a perfect fit.
CNC Machining vs. 3D Printing
While both CNC machining and 3D printing are digital manufacturing methods, they differ significantly:
Feature | CNC Machining | 3D Printing |
Method | Subtractive | Additive |
Material Range | Wide | Limited (though expanding) |
Precision | Very High | Moderate to High |
Speed for Prototypes | Faster for simple parts | Faster for complex parts |
Surface Finish | Superior | Requires post-processing |
Ideal For | Metals, production parts | Plastics, prototypes |
Both have their place in modern manufacturing, and many companies use a hybrid approach—prototyping with 3D printing, then switching to cnc machining for final production.
Choosing a CNC Machining Partner: Key Considerations
Outsourcing cnc machining can save time and capital, but selecting the right partner is crucial. Here’s what to look for:
✅ Technology & Equipment
Make sure the provider uses advanced machines (like 5-axis mills) and has a wide range of capabilities to handle diverse geometries and materials.
✅ Quality Certifications
Look for ISO 9001, AS9100 (aerospace), or ISO 13485 (medical) to ensure consistent manufacturing practices.
✅ Material Expertise
A good supplier should advise on material selection based on your application’s mechanical, thermal, and chemical requirements.
✅ Prototyping and Production
Can the partner scale from single prototypes to thousands of units? Agility matters in today’s fast-moving markets.
✅ Customer Support
Transparent communication, design feedback, and post-sale support are signs of a reliable and service-oriented partner.
CNC Machining Trends in 2025 and Beyond
As manufacturing continues to evolve, cnc machining is also advancing through:
- Smart Factories and IoT: Machines are increasingly connected, enabling predictive maintenance and real-time production data.
- AI-Driven Toolpaths: Artificial intelligence is helping optimize cutting strategies for faster and more efficient material removal.
- Automation & Robotics: CNC machines now work alongside robotic arms to automate entire production lines.
- Sustainable Practices: More shops are using eco-friendly coolants, recycling metal chips, and reducing energy consumption.
Embracing these trends allows businesses to remain competitive while lowering operational costs and improving sustainability.
Final Thoughts
From prototyping an innovative new product to producing mission-critical aerospace components, cnc machining is an indispensable manufacturing solution. Its blend of speed, precision, versatility, and cost-effectiveness makes it the go-to choice for modern engineers, product designers, and manufacturers.
By understanding its capabilities and selecting the right machining partner, companies can shorten development cycles, ensure part reliability, and gain a true edge in their markets. Whether you’re a startup launching a new gadget or an enterprise seeking a scalable manufacturing process, CNC machining is an investment in quality, efficiency, and long-term success.