Role of an Aluminium Circle Manufacturer in Modern Industry
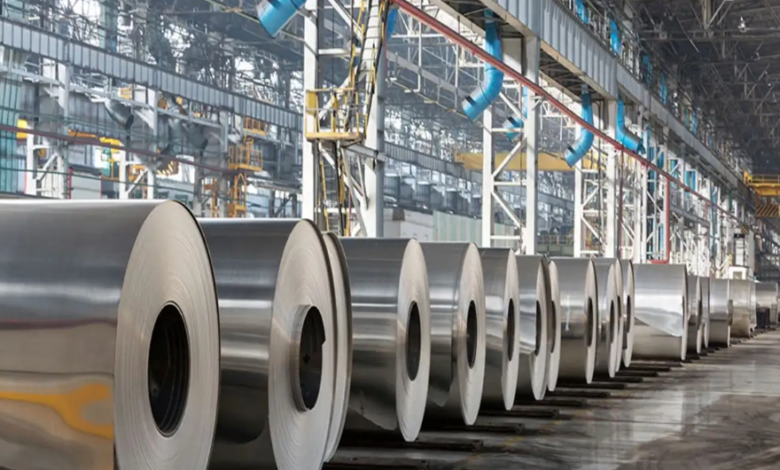
Introduction
Aluminum has long been valued for its light weight, corrosion resistance, and versatility. Among the various aluminum products in the global market, aluminium circles play a critical role in many industries such as cookware, lighting, automotive, and electronics. Behind every high-quality aluminum disc lies a skilled and experienced aluminium circle manufacturer dedicated to precision and innovation. This article explores the essential functions, production processes, applications, and advantages offered by these manufacturers.
What Are Aluminium Circles?
Aluminium circles, also called aluminum discs or blanks, are flat, round pieces cut from aluminum coils or sheets. They are typically used in deep drawing and spinning processes due to their excellent ductility and thermal properties. The size, thickness, alloy composition, and surface treatment of these circles vary depending on their intended use.
These products must meet strict dimensional tolerances and surface quality standards, which is why selecting the right aluminium circle manufacturer is essential for businesses that rely on them.
Manufacturing Process
An aluminium circle goes through a series of carefully controlled steps before it is ready for use:
- Raw Material Selection: High-quality aluminum ingots are melted and cast into slabs. Common alloys include 1050, 1060, 1100, 3003, and 5052.
- Rolling: These slabs are hot rolled and then cold rolled into thin sheets or coils.
- Blanking: Using CNC-controlled machines or punching equipment, the aluminum sheets are cut into precise circles.
- Annealing: The blanks are softened through heat treatment, which enhances their formability.
- Surface Cleaning: Oil and impurities are removed through chemical or mechanical cleaning to ensure a smooth finish.
- Quality Inspection: Every batch undergoes rigorous tests for thickness, diameter, hardness, and surface finish.
A reliable aluminium circle manufacturer ensures consistency and accuracy at every stage to meet both domestic and international standards.
See also: What’s Involved in Transportation and Logistics for Businesses
Applications in Cookware
One of the largest markets for aluminum circles is the cookware industry. Cookware manufacturers prefer aluminum discs because they offer:
- Excellent heat conductivity
- Even heat distribution
- Non-toxic and food-grade properties
- Light weight and ease of shaping
Aluminum circles are used to make frying pans, pressure cookers, baking trays, and other utensils. The deep drawing ability of certain aluminum alloys allows manufacturers to form complex shapes without cracking or losing strength.
A trusted aluminium circle manufacturer understands these requirements and supplies pre-treated, scratch-resistant, and even color-coated circles for added value.
Use in Lighting
The lighting industry also relies heavily on aluminum circles to make reflectors and lamp housings. Aluminum’s high reflectivity makes it ideal for directing light efficiently. Discs used for lighting must be smooth, polished, and dimensionally stable.
Manufacturers often offer customized solutions such as:
- Anodized surfaces
- Mirror finish circles
- Colored coatings for decorative lighting
Top manufacturers also support OEM and ODM lighting product designs, helping businesses bring new ideas to market faster.
Role in Automotive and Electronics
In the automotive industry, aluminum circles are used to produce fuel tank covers, brake parts, and interior components. Their lightweight properties contribute to better fuel efficiency and lower emissions. Electronics manufacturers also use them in battery enclosures and speaker diaphragms.
To meet the rigorous demands of these industries, an experienced aluminium circle manufacturer must offer:
- Precise mechanical properties
- Consistent thickness
- Corrosion resistance
- Thermal stability
They may also need to comply with industry-specific certifications such as ISO/TS 16949 for automotive components.
Customization and Flexibility
Different industries require different aluminum circle specifications. A well-established manufacturer offers extensive customization options:
- Thickness range from 0.3 mm to 8 mm
- Diameters from 50 mm to 1200 mm or more
- Various tempers (O, H12, H14, H18)
- Surface treatments like anodizing, brushing, or polishing
- Laser marking or logo etching for brand identity
These customization capabilities make an aluminium circle manufacturer an essential partner for companies looking to optimize production and reduce waste.
Importance of Quality Control
When choosing a supplier, quality is non-negotiable. Aluminum discs that are inconsistent in size or temper can lead to poor end-product performance or damage during forming. Therefore, top manufacturers implement stringent quality control systems including:
- Spectral analysis to confirm alloy composition
- Micrometer and caliper checks for thickness and diameter
- Surface flaw detection
- Mechanical testing for tensile strength and elongation
They also maintain traceability records, ensuring that any issues can be traced back to specific batches.
Global Supply Chain Capabilities
Today’s aluminium circle manufacturer often serves customers across the globe. This means they must have strong supply chain capabilities, including:
- International certifications like ISO 9001 and SGS
- Efficient packaging and labeling
- Partnerships with freight forwarders
- On-time delivery systems
- Multilingual sales support
Manufacturers with these capabilities help businesses maintain consistent production schedules and reduce downtime.
Focus on Sustainability
Environmental responsibility is a growing concern across industries. Forward-thinking manufacturers adopt eco-friendly practices such as:
- Using recycled aluminum
- Energy-efficient smelting and rolling
- Wastewater treatment systems
- Low-emission annealing processes
These efforts not only reduce environmental impact but also appeal to clients with sustainability goals. Partnering with a green-certified aluminium circle manufacturer enhances a brand’s corporate social responsibility image.
Choosing the Right Manufacturer
Selecting the right manufacturer can make a significant difference in product performance, cost, and delivery times. Here are some tips for choosing a reliable aluminium circle manufacturer:
- Check Experience – Look for companies with a long history in aluminum processing.
- Inspect Certifications – Ensure they hold relevant industry and quality standards.
Conclusion
Aluminium circles may seem like simple components, but their manufacturing involves precision, expertise, and innovation. From cookware to lighting, and automotive to electronics, these discs serve as the backbone of many products we use daily. Choosing a dependable aluminium circle manufacturer ensures access to high-quality, customizable, and cost-effective materials that meet both performance and environmental standards.
As industries evolve and demand rises, partnering with a skilled manufacturer becomes more than a transaction—it becomes a strategic collaboration that fuels growth and innovation.